PRODUCTIVE PROCESS
From raw metal to finished product
In our factory we carry out all the processes of the production chain, following strict quality controls to comply with the standards required by the markets and customers.
Design
Using computer design software, we create three-dimensional and two-dimensional models, which will guide the numerically controlled machinery.See more
Forging
By exerting pressure, the machinery compresses the incandescent metal using molds that guarantee cutting uniformity and working speed.See more
Numerical control machinery
With our numerically controlled machinery, we carve brass by exporting material to obtain a wide range of semi-finished pieces.See more
Carving
The metal is carved with high precision numerical control machines to give it the shape required by the piece.See more
Laser cut
We cut metal with millimeter precision machines that perform computer-controlled series laser cutting.See more
Welding
The individual components are hand welded to each other by skilled operators with decades of experience to form the final piece.See more
Vibration
By eliminating surface imperfections and smoothing the piece, the vibration, made with abrasive material, guarantees the high qualityrequired by the sector.See more
Galvanic
The pieces, through supports, are immersed in tanks with chemical solutions inside that give the metal additional mechanical and decorative properties.See more
Glazing and stressing
Small amounts of enamel or rhinestones are inserted inside the cracks of the piece to give it color and elegance.See more
Polishing
In the final stage of production, the piece is mirror polished by rollers sprinkled with polishing material and waxes, to ensure clarity.See more
Quality check
We analyze and test the pieces with the use of the most modern tools for qualitative investigations, thus respecting all the strict rules required by the market.See more
Packaging
The finished product, after a careful check, is packaged and placed in elegant boxes to then be sent to customers.See more
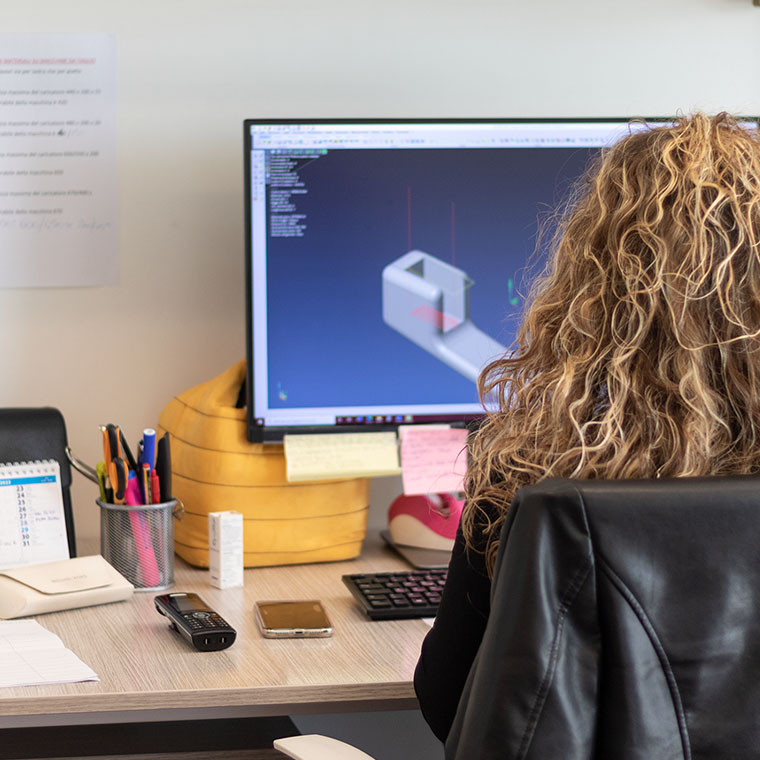
Design
Our company transforms ideas into “industrialized” articles with “artisanal” care. The design processes are carried out within our sophisticated laboratories.
According to the guidelines dictated by the customer, with 3D design programs, an expert technical team creates a prototype on the computer for the pieces that will then be forged in the subsequent stages of the production line.
Forging
Hot forging of metal has multiple advantages, both in terms of material integrity and absence of imperfections.
Our supply chain equipped with highly technological systems is able to meet the quality standards required by the customer on the final product.
All the processing steps of hot forging are carried out by highly qualified personnel, to optimize the production process to the maximum and at the same time maintaining a level of quality that is always high and constant over time.
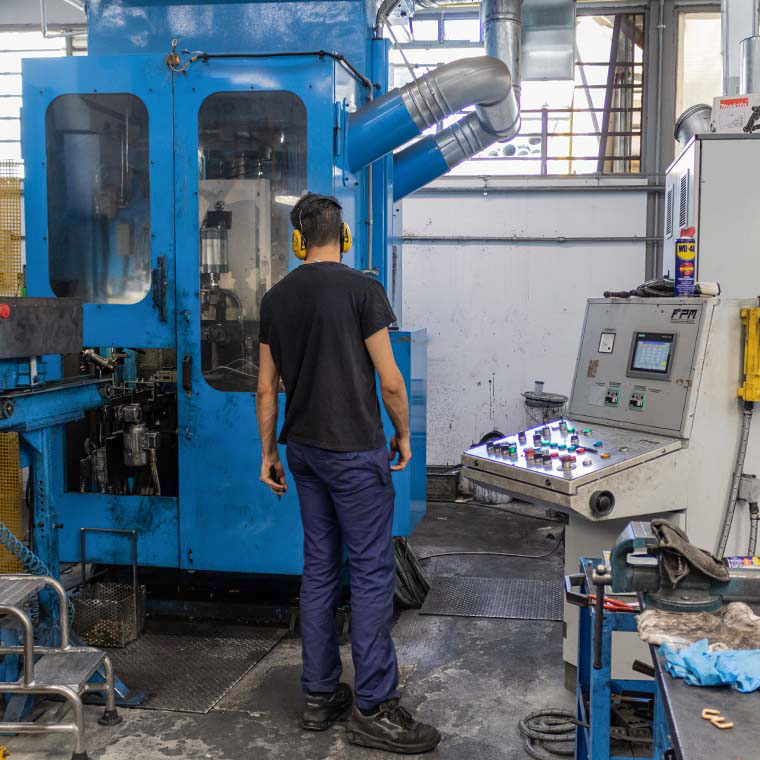
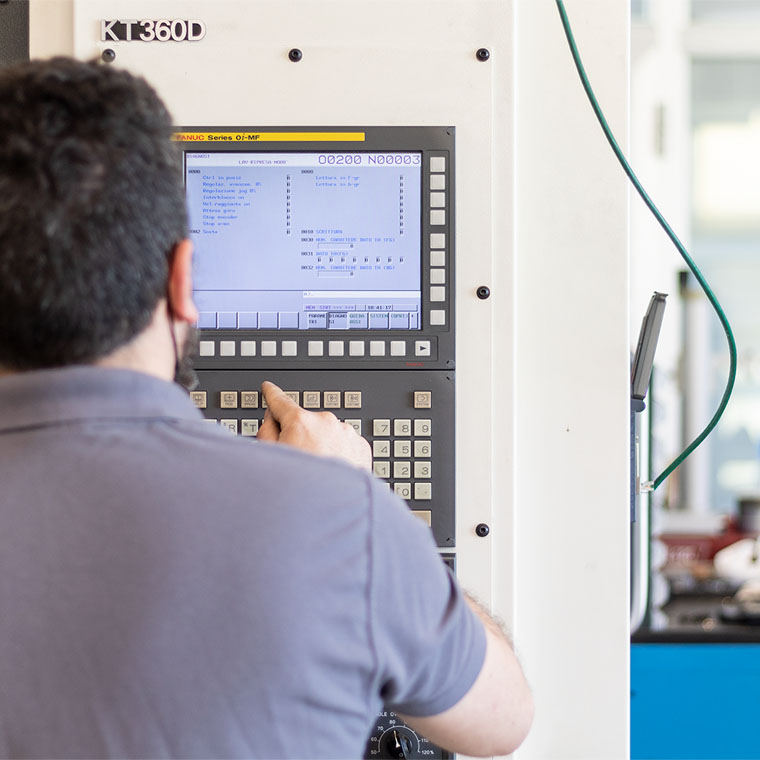
Numerical control machinery
Using the latest generation CNC machinerywe produce extremely precise parts at different tolerance options. The machine carves the pieces starting from the block of material using a subtractive machining process with 3 or 5 axis milling. The sharp edges of the machined pieces will be subsequently removed according to the standard vibrating procedure.
Carving
In our factories we use numerically controlled machinery for carving. After carrying out a preliminary roughing of the metal where material is removed in a rather coarse way, we proceed with the finishing in which the piece is modeled to measure in order to reduce it to the desired shape, size and roughness.
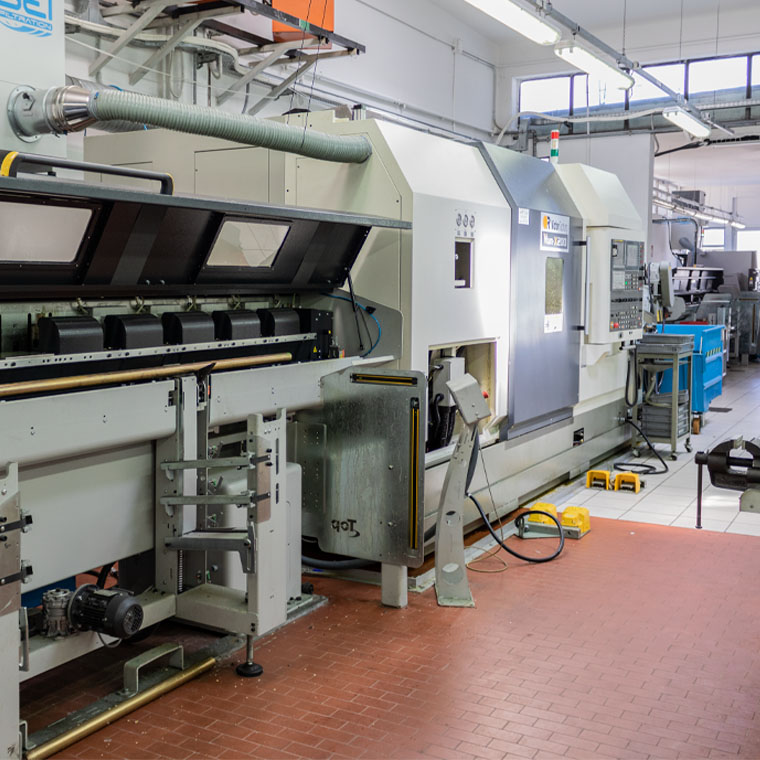
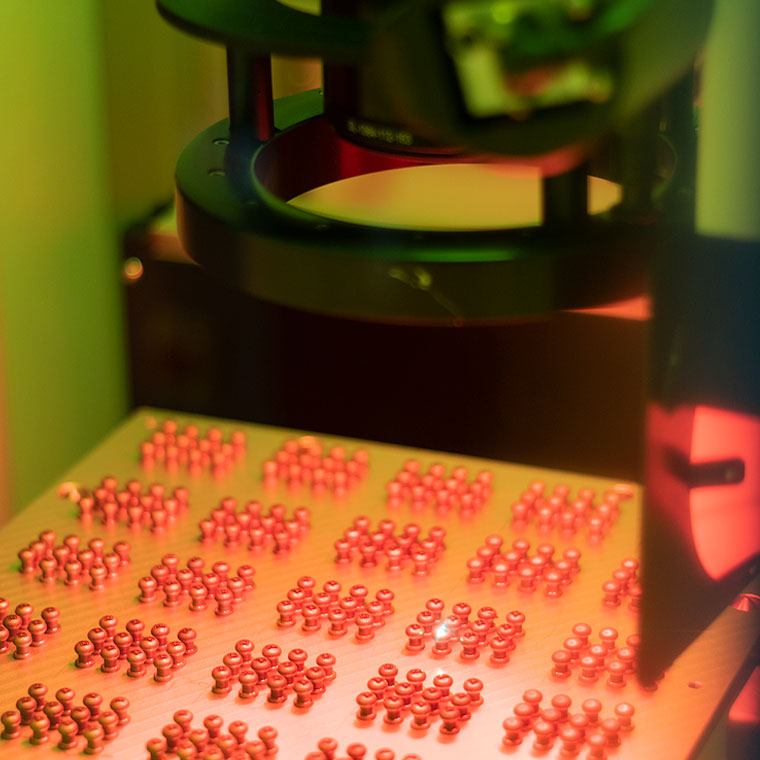
Laser cut
CNC laser cutting is a PC controlled manufacturing process that uses a high density beam of light to cut parts from a piece of metal.
The process is guided by a computer in accordance with the templates preloaded by the design laboratory. With this process, we are able to guarantee very high precision laser cuts.
Welding
In the welding department, the pieces are melted together to compose the raw product which must then be finished.
The processes are mostly still carried out manually by traditional welding, performed by highly specialized workers in metal welding.
Technology, even the most advanced, needs craftsmanship. In metalworking, there are some steps that require the expert hand of those who know the trade, without sacrificing precision and quality.
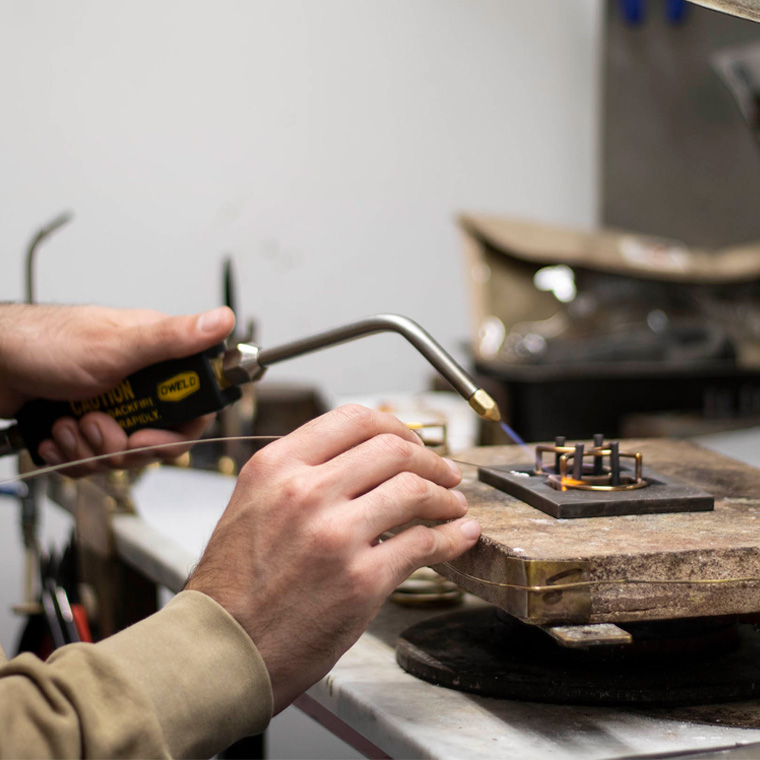
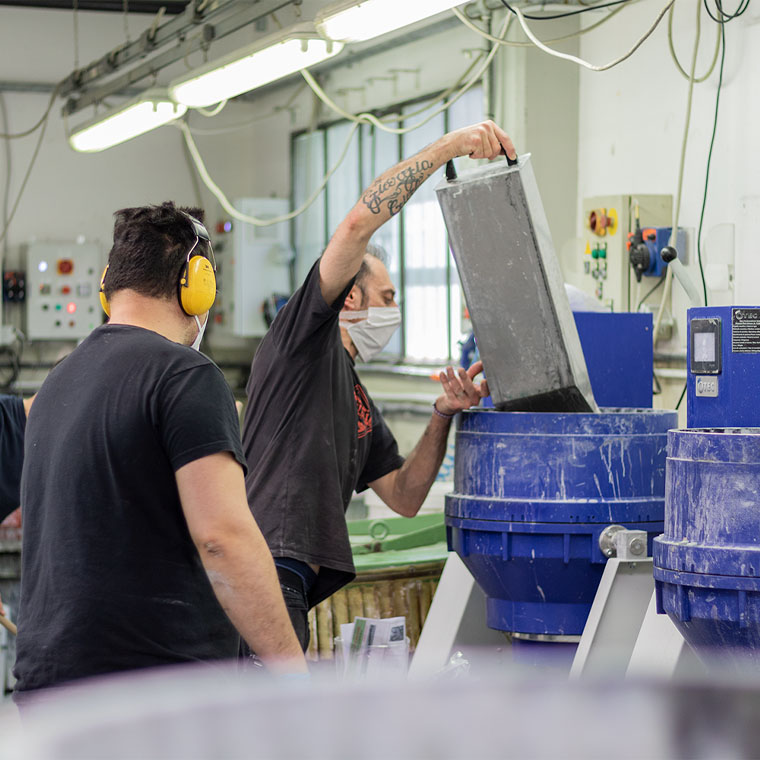
Vibration
Vibration is the technique that allows you to remove the final imperfections, smoothing, polishing and cleaning the metal components. During the process, the pieces are placed in vibrating tanks inside which there are abrasive plastic or ceramic materials.
After various stages in which the product will pass into tanks with an increasingly finer grain, it will be clean and smooth to perfection.
Our state-of-the-art vibrating department allows you to process large quantities of product and at the same time guarantees a high final quality.
Galvanic
In our latest generation galvanic department, through chemical processes obtained by immersion in metallic solutions, we deposit on the surface of the pieces, a thin layer of a metal or a noble alloy that modifies their properties, from a decorative and technical point of view, improving for example the characteristics of resistenza alla corrosione e le mechanical, electrical and optical properties.
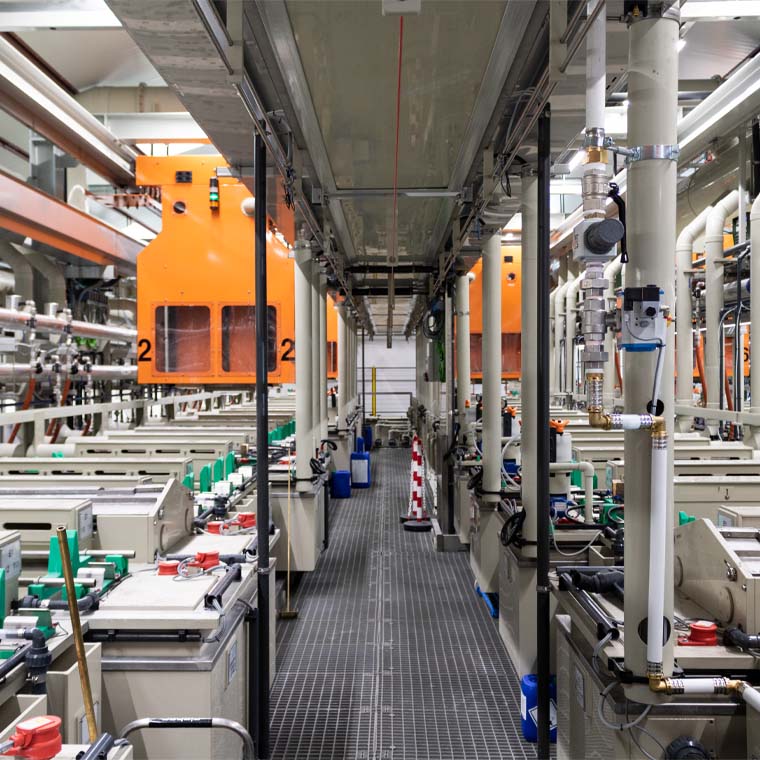
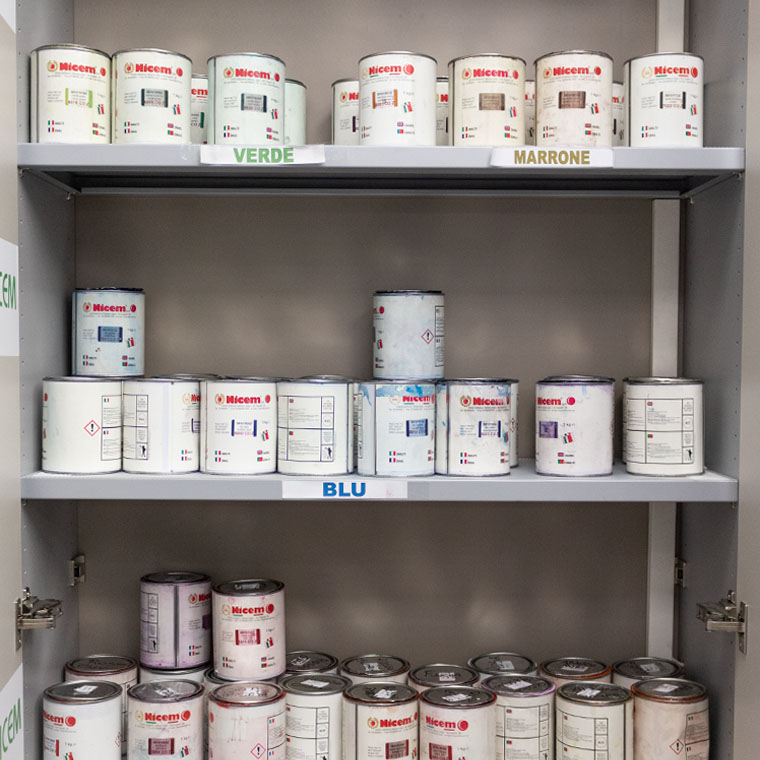
Glazing and stressing
Enamelling is one of the techniques for coating metal surfaces. It is used to decorate the pieces and give color.
In our departments we use both hot and cold enamelling techniques.
We have many colors that can be mixed together, thus guaranteeing the customer a wide range of choice.
Polishing
The final polishing of the piece before being packaged. The continuous search for a quality product has led the company to set up a department dedicated to cleaning. This allows us to obtain the highest quality and different finishes.
The polishing process is carried out by applying the piece against a moving abrasive, to go from a rough piece with roughness to a perfectly clean mirror-like material.
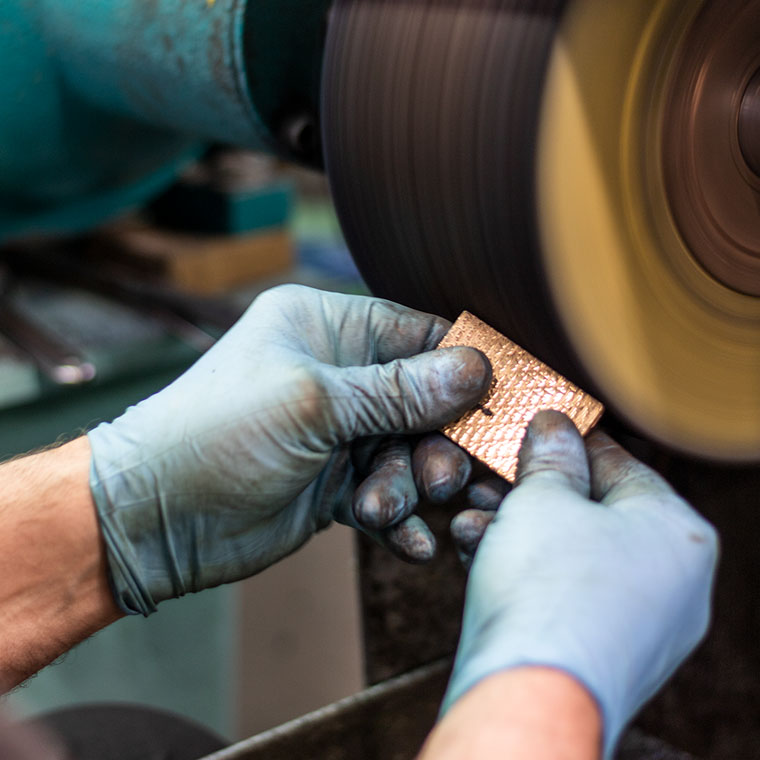
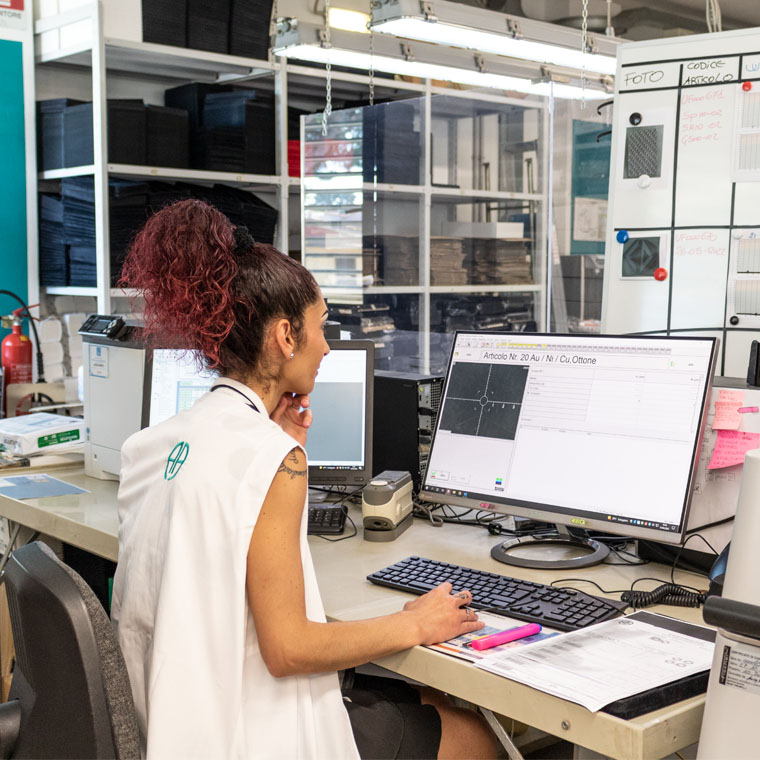
Quality check
Assembly and packaging
The packaging of the finished product is still carried out by hand, just as it was once done, to minimize the risk of damage to the piece. The attention to the smallest details that we place even in this phase is dictated by the high standards that the markets require. After a final polishing, the labels and certificates of conformity are applied to the pieces, then they are arranged in elegant boxes that will be delivered to customers.
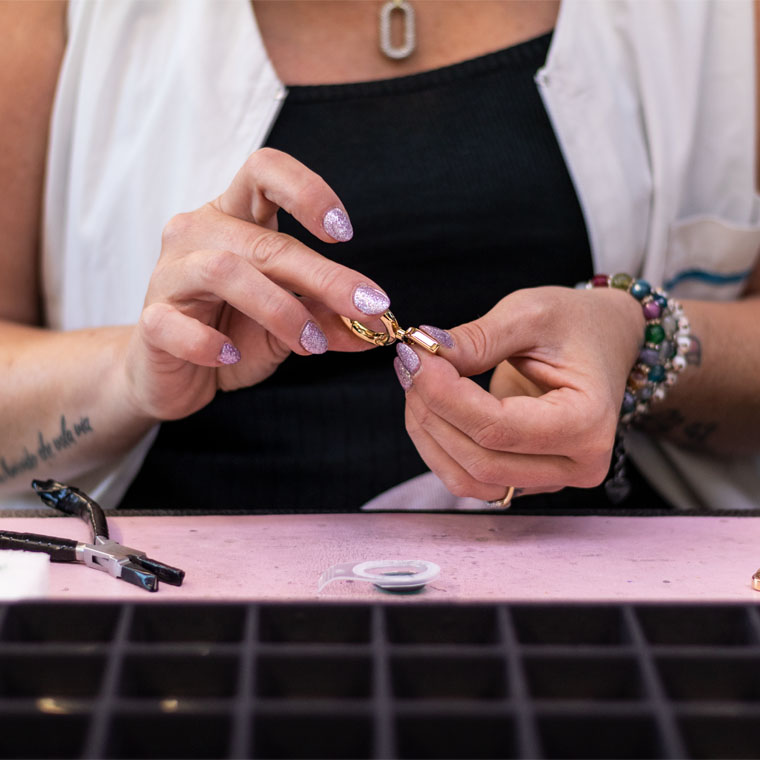